HOT PIPE COATING is designed to control heat transfer on surface temperatures up to 450F (232C). It is waterborne and extremely lightweight in appearance. HOT PIPE COATING offers a “Green”, non-flammable, non-toxic formula for high temperature surface applications.
HOT PIPE COATING has been engineered to be applied directly over hot surfaces for instant adhesion without the need for costly shutdowns. HOT PIPE COATING is waterborne to offer a non-flammable, non-toxic formula for high heat situations.
HOT PIPE COATING replaces conventional jacket insulation to provide superior insulation, corrosion under insulation and personal protection. CUI is common threat to all industries around the globe. HOT PIPE COATING revolutionizes the way we think about high heat insulation for both above and below grade pipes, tanks, furnaces, boilers, heat exchangers and more. The ease of application and inspection is what wins over owners, inspectors, and applicators alike.
- Performance – 0.06 W/mK conduction ASTM C177
- Single Component – no mixing part A & B
- Safe – non-flammable, class A rated
- Easy to Apply – no shutdown, heat cured
- Surface Tolerant – minimal surface preparation, no primer needed
- CUI Protection – resists moisture, prevents CUI
- Personal Protection – cool to touch
- Inspection – easy to inspect and remove
- Durable – can withstand rail/hail storms
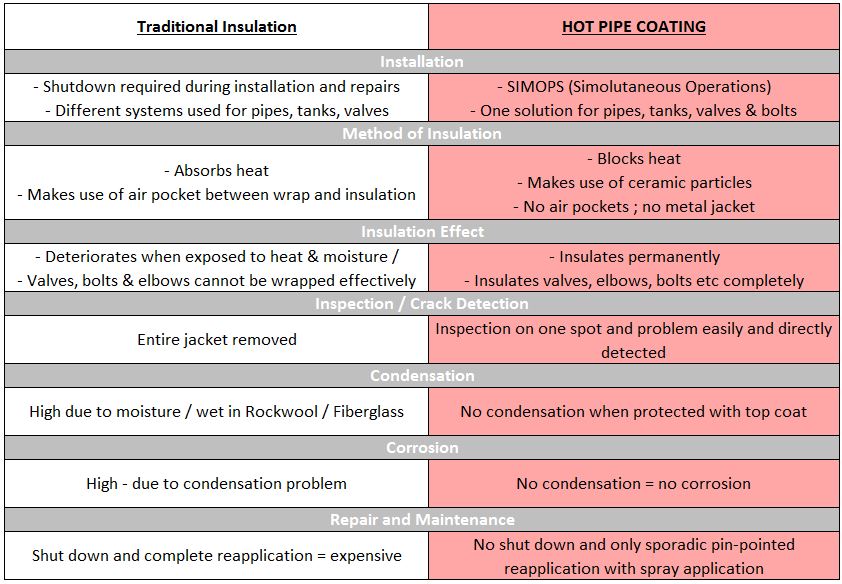
For Technical, Application & SDS files please click below.
HPC-Coating-Product-Documents-11-05-19
Hot Pipe Coating (HPC) insulation method is completely different than the conventional insulation wrap, which only slows down the loss of heat, mainly through the air space between the jacket.
HOT PIPE COATING’s unique blend of eight ceramic compounds create a barrier to catch and hold heat on the surface of the unit (e.g. pipe, furnace, boiler, heat exchanger, etc.) This can be directly observed by the correlating rise in metal temperature behind the coating film. Unlike wraps that use air as the insulation component, the low density ceramic compounds in HOT PIPE COATING traps and holds the heat onto the surface for more effective insulation performance.
HOT PIPE COATING has a combination of high temperature resistant resins. This coating will dry by evaporation. Curing can be accelerated through heat in the environment or the surface.
CONVENTIONAL JACKET INSULATION vs HOT PIPE COATING (HPC)
Corrosion Under Insulation is a common threat faced by multiple industries across the globe. Clients who have hot processes / assets fully understand the cumulative cost associated with the use of metal cladding including rock-wool, mineral wool, calcium silicate, fiberglass, etc. Conventional jacket insulation have resulted in unnecessary cost, mainly associated with, Corrosion Under Insulation (CUI), high energy costs, production inefficiencies, shut downs for scheduled maintenance and asset replacement which impacts profitability and shareholder’s value in a negative manner.
HPC AND HPC-HT solutions can solve all the above problems, in a manner that is both measurable and verifiable.
Metal jacketing / cladding systems are very energy inefficient and prone to CUI. When these materials are used in real world application with metal cladding, the insulation materials are merely wrapped around the hot pipe or surface, always leaving an airspace / gap between the hot pipe and the insulation. Within this small air space and gaps, a tremendous amount of heat energy in BTUs escape from the hot surface and ultimately it is absorbed into and migrate through the insulation material, where it dissipates within the metal cladding. This gives the illusion that the surface is well insulated within the cladding, when in reality, a tremendous amount of energy / BTUs ultimately escape from the surface and are lost. The only insulation is actually just air space between the hot pipe and the jacket.
When HPC is used for hot applications, it is spray applied directly to the hot pipes, tanks, valves or elbows. Once cured, HPC is fully adhered, and there are no air space or gaps between the HPC and the hot surface, which significantly enhances energy conservation, as the heat / energy cannot escape off the hot surface. HPC is designed using 7 specific low density ceramic materials that are designed to hold the heat on the hot surface and to BLOCK heat loss. This can be measured and verified through a rise in INTERNAL temperature within the pipe or tank and the external surface skin temperature rising to almost the same temperature.
In comparison, metal cladding systems have a questionable track record in terms of energy inefficiencies and development of CUI because they are not air & moisture tight. These deficiency will cost companies a significant amount of revenue with both shut downs and total lifetime asset protection costs. HPC on the other hand, resists moisture infiltration and is designed for longevity. HPC is sprayed on with instant adhesion, direct to the hot surface, where it is allowed to dry. After drying, HPC is sealed with one of our specific top coats that have no pores and do not breath, (SP Seal Coat HT recommended). This ensures that the HPC insulation stays air tight & is moisture free, which prevents CUI.
Additionally, metal cladding systems require shut downs when visual inspections are due. This is not the case when HPC is used on hot surfaces, as visual inspections are done live plant while the system is hot and operational, by simply using a box cutter to cut through the HPC system down to the metal surface, visually inspect the substrate and then trowel HPC back into the cut out (as HPC is self-healing) and apply the top coats. Ultrasound may also be used when doing inspections.
Lastly, unlike metal cladding systems, HPC is applied on live assets, which again does not require a shut down, thus providing additional savings. HPC also provides personal protection on par with any insulation jacket.
Factoring the savings alone from avoiding a shut down when applying HPC, plus simplified visual inspections, more than pay for the cost of HPC application. Additionally, there is no CUI development as a result of reduced moisture infiltration. HPC also improves energy conservation when compared to metal cladding because with HPC there are no air gaps for moisture infiltration. Ease of application and inspection combined with an average material cost payback in terms of energy savings of 8-12 months makes HPC the smart choice hot asset insulation.
HOT PIPE COATING, with its immediate adhesion, is designed to control heat transfer on surface temperatures up to 370°C. Please find below a few selected references from our Global Database intended to show the type of application, solution and markets in which HOT PIPE COATING has successfully been applied: